Managing construction costs is crucial for contractors to deliver projects on budget and maximize profits. With expenses for materials, labor, and equipment continually rising, implementing cost-saving strategies has become essential. This article outlines 12 proven tips contractors can use to reduce expenses on their building sites without compromising quality.
1. Buy Construction Materials Strategically
Strategically purchasing construction materials can lead to significant cost savings for contractors:
- Buy materials in bulk quantities to get volume discounts compared to incremental purchases
- Work with wholesale distributors to get lower prices than at retail stores
- Thoroughly shop around and compare prices online before purchasing
- Look for deals, discounts, and incentive offers for large purchases
- Properly store bulk purchases in clean, dry areas to prevent weather damage
- Keep an organized inventory system to optimize the use of materials already on hand
- Coordinate with subcontractors to efficiently share excess materials between jobs
- Take advantage of just-in-time delivery to reduce storage costs
Buying materials deliberately in this way ensures contractors get the lowest possible pricing. Proper planning, storage, and coordination of material purchases and inventory provides savings on every construction project.
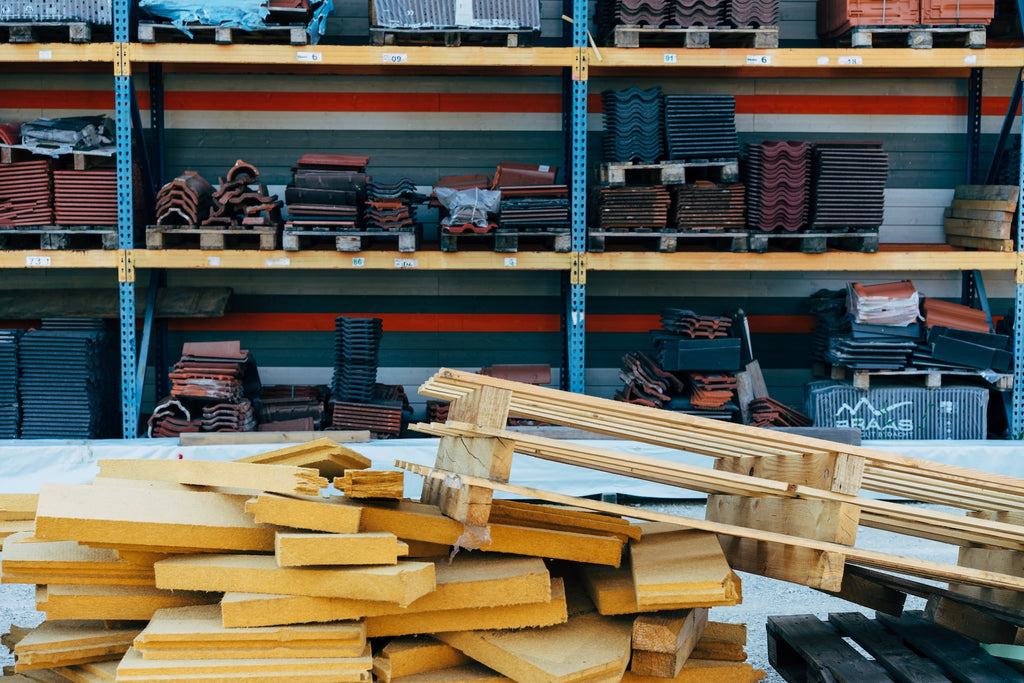
2. Optimize Site Management and Efficiency
Carefully managing the worksite and maximizing efficiency reduces waste and saves on labor costs:
- Invest in power tools like trenchers to speed up digging, earthmoving, and other tasks
- Closely track worker productivity and keep everyone on task
- Reassign crews to interior tasks if weather halts exterior work
- Position materials strategically to minimize excess movement around the site
- Streamline workflows and processes to reduce wasted time and expenses
- Encourage crews to identify areas for improvement in efficiency
- Provide adequate supervision and project management
- Quickly address any deficiencies or bottlenecks in productivity
Smooth site operation and optimization of labor output reduce expenses and keep the project on budget.
3. Invest in Durable, High-Quality Tools
The tools used on a construction site see tough conditions and heavy use. Purchasing high-quality, durable tools, even at a higher upfront cost, saves money over time. Quality tools last longer through rigorous work compared to inexpensive options. This reduces the frequency of having to replace broken or faulty equipment.
When buying tools, research available warranties and keep detailed records. Making warranty claims on defective tools provides additional cost savings. Well-maintained quality tools lead to long-term savings.
4. Rent Equipment When Possible
For equipment and machinery used only periodically, renting is often the most cost-effective option compared to purchasing. Renting is ideal for heavy machinery like excavators, backhoes, cranes, or loaders needed just for specific jobs. Compare the short-term rental fees for the equipment with the costs of long-term ownership, including maintenance, transportation, and storage fees. For occasional use, renting equipment minimizes expenses.
5. Reduce Material Waste
Construction waste management is another key area with big potential savings. Reuse and recycle materials already onsite whenever possible. Choosing construction products with minimal packaging or bulk options reduces overall waste. Avoid inefficient site layouts that lead to excessive movements, causing wasted time, labor, and materials.
Carefully schedule crews to minimize standby time waiting for other workers and tasks to be completed. Proper planning and careful coordination of manpower and sequencing of interdependent tasks can help avoid wasted standby time and result in cost reductions.
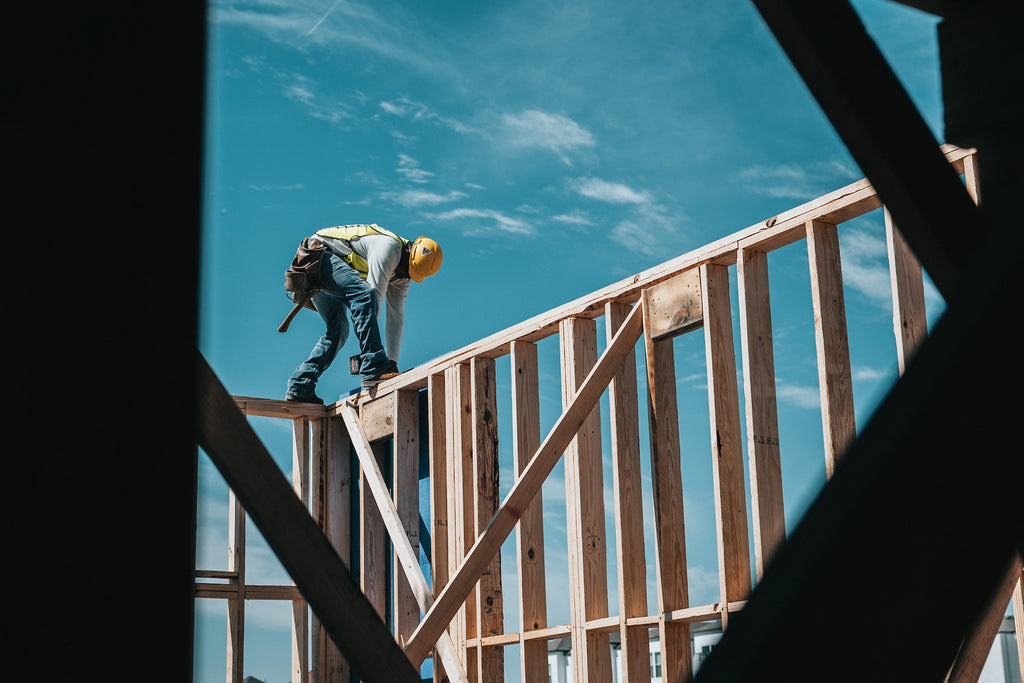
6. Comparison Shop Subcontractor Bids
Don't just automatically go with your normal subcontractors. Occasionally solicit bids from new service providers to compare pricing. Consider experience, reputation, equipment, and safety record when comparing bids rather than choosing the lowest figure. Building relationships with subcontractors through negotiated rates and guaranteed future work can yield lower bid pricing.
7. Regular Equipment Inspection and Maintenance
Consistently inspecting equipment and performing preventative maintenance extends the working life of tools, vehicles, and machines used onsite. Catch minor issues before they escalate into bigger problems requiring expensive repairs. Track tools being used on the site and have a check-out system to prevent loss.
Selling used equipment to workers at cost or incentivizing workers to supply their own tools are other great strategies to get quality tools onsite at low costs. Well-maintained equipment helps minimize replacement costs.
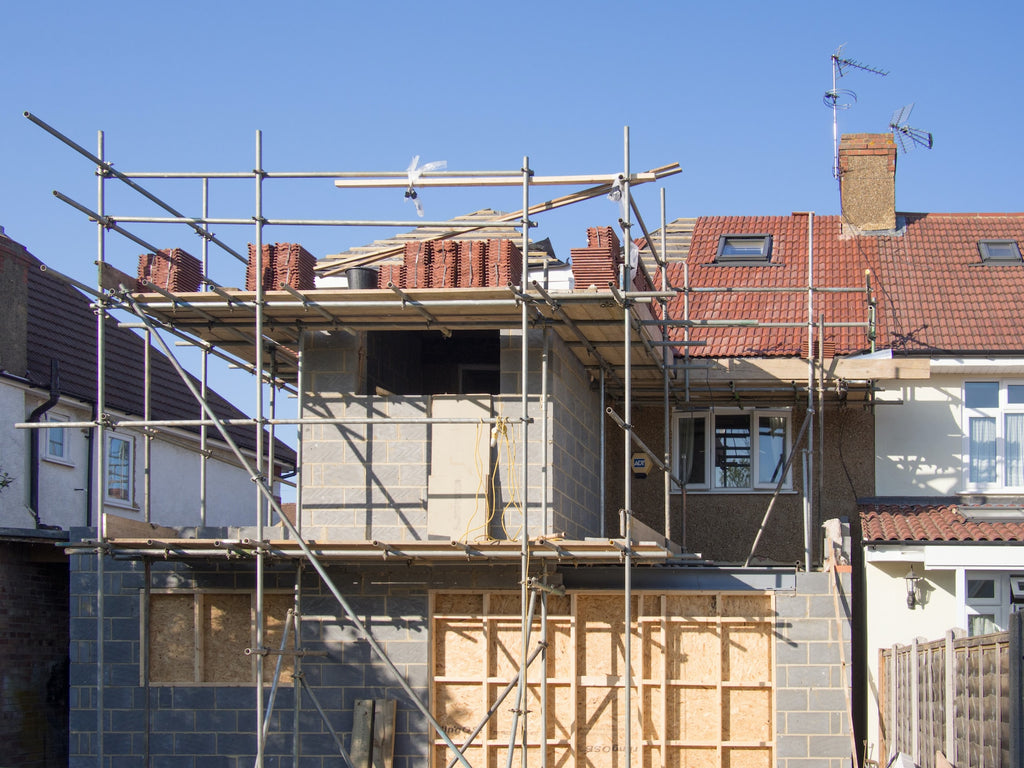
8. Use Technology to Increase Efficiency
Implementing the right technology can lead to major efficiency gains and cost savings:
- Invest in software tools for scheduling, logistics, paperwork, and overall project management. Streamline cumbersome manual processes.
- Use GPS and fleet tracking to optimize vehicle routing and utilization. Reduce mileage and fuel costs.
- Automate paper-based submissions, reports, and approvals through digital forms and workflows. Save time and labor.
- Choose user-friendly software and provide training to workers to ensure smooth adoption. Overcome resistance to change.
- Evaluate new technologies like drones, 360 cameras, and virtual/augmented reality for potential applications.
- Implement equipment telemetry to track usage hours and optimize maintenance. Prevent breakdowns.
- Digitize blueprints and project documents for easy access and sharing across sites. Reduce errors.
Strategically leveraging the right technologies provides tangible productivity gains and cost savings on construction projects.
9. Negotiate Costs Upfront
When starting a new project, take time to negotiate costs upfront with suppliers and subcontractors, even if you have existing relationships with them. Offer incentives like guaranteed future work or volume discounts in exchange for the best pricing deals. Make sure to clarify change order approval processes clearly in the contract language to avoid unexpected expenses popping up later down the road. Try to develop cooperative partnerships with vendors rather than just treating them as one-off transactions. Being proactive early on about pricing and agreements provides the most favorable terms.
10. Use Floor Protection Products
An often overlooked area for potential savings is properly protecting project floors during construction. Investing in quality floor protection products like Spriteshield floor protectors minimizes expenses for repairs and replacements caused by heavy equipment, foot traffic, spills, and scrapes. Floor protection allows easy access to subfloors for wiring and plumbing modifications without damaging surfaces.
Reusable floor protection boards provide long-term savings compared to paper alternatives. Installing protection early in the process prevents damage before drywall and flooring are in place. Proper floor protection reduces cleanup time and creates smoother workflows.
11. Implement Stringent Site Security
It's essential to implement stringent security measures on construction sites to prevent expensive losses from theft, vandalism, and accidents. Make sure to have adequate perimeter fencing, lighting, surveillance cameras, and access control systems in place that deter potential threats. Conduct regular maintenance and diligently update any security equipment to fix vulnerabilities quickly. Instead of only relying on live onsite guards, consider utilizing remote monitoring services to provide cost-effective 24/7 coverage without lapses in protection. Solid security boosts safety, prevents disruptive breaches, and reduces the need for costly damage corrections down the line.
12. Carefully Manage Accounts Payable and Receivable
Staying on top of both accounts payable and accounts receivable is key for optimizing cash flow and keeping projects running smoothly. Be diligent in sending out invoices right away upon completing project milestones, follow up on any outstanding payments, and think about offering incentives for early payment. Avoid excessive upfront costs by staggering material purchases based on scheduled use. Consistently tracking expenses, maintaining financial transparency, and sticking to budgets helps contain costs. Keeping a close eye on financial accounts reduces avoidable costs and cash flow issues.
Conclusion
With proper planning and execution, contractors can implement these cost-saving tips without sacrificing quality or safety. Strategically reducing expenses leads to optimized profits and competitive bidding advantages. The construction business involves narrow profit margins, making effective cost containment necessary for success. These practical low-cost strategies allow construction projects to run lean.
Leave a comment
All comments are moderated before being published.
This site is protected by hCaptcha and the hCaptcha Privacy Policy and Terms of Service apply.